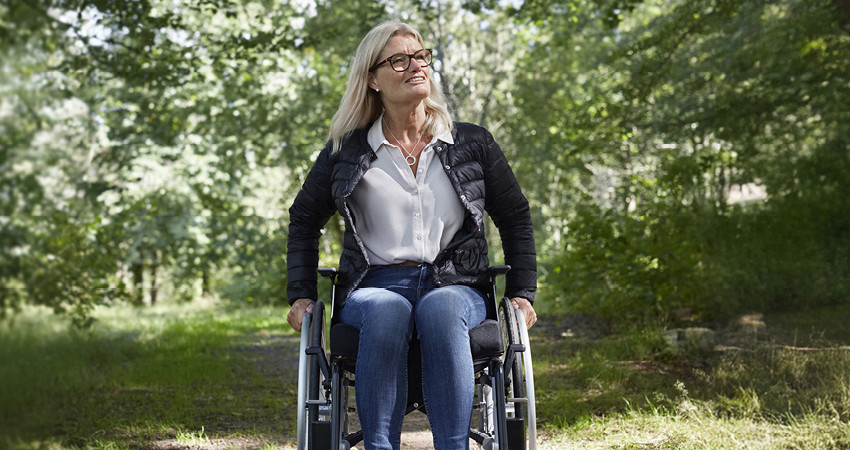
Early research project confirms re:vive’s climate benefits
Up to 50% saved emissions by remanufacturing
A life-cycle assessment of Etac’s re:vive concept has indicated that a wheelchair that is remanufactured to further extend its lifetime can save up to 50% emissions compared to a completely new wheelchair, even after factoring in the transportation emissions to and from the remanufacturing site.
A student team at Linköping University in Sweden performed detailed calculations of the carbon emissions impact of a new Etac Cross wheelchair – including extraction and production of the raw materials – versus one that has been remanufactured through Etac’s re:vive program. Even taking into account worst-case scenarios for transporting the wheelchair from Etac’s sales unit in the Netherlands to Etac’s remanufacturing site in Anderstorp, Sweden, and back again, the remanufactured wheelchair had far lower carbon emissions than a new product.
The student team worked with Etac and based the life-cycle assessment on Etac’s first re:vive customer Medux, in the Netherlands. “Medux, as a forward-thinking and innovative collaboration partner, has been very helpful to us in developing our remanufacturing concept re:vive,” said Marika Törnqvist, Head of Product Management for Etac wheelchairs.
By remanufacturing and keeping a wheelchair in a circle of re-use for as long as possible, both Etac and the customer can contribute to reducing carbon emissions, the analysis indicated. If the entire wheelchair is remanufactured – versus replacement of some parts – the emissions savings can be as high as 50% of those of a new wheelchair.
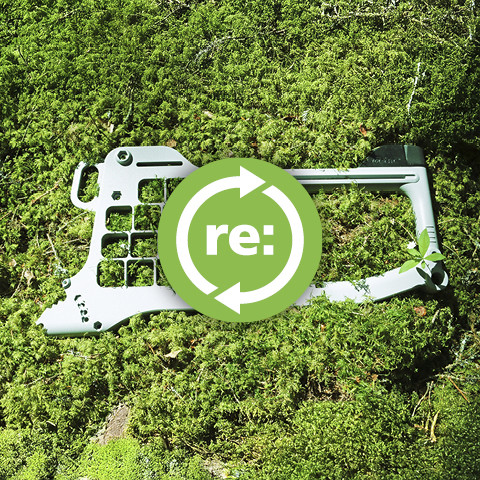
The main reason for the savings in the remanufacturing concept is related to the aluminium, which comprises around 60% of the wheelchair’s weight. Extracting aluminium and producing metal parts is highly energy-demanding and accounts for most of a new wheelchair’s carbon emissions. However, once in place, the metal can be reused indefinitely, providing significant benefits to remanufacturing
“The early life-cycle assessment confirmed that we’re on the right track in increasing our marketing efforts for re:vive. We know our products are built to last and that we can extend their lifespan through remanufacturing,” said Marika Törnqvist.
At Medux, we see this as a strong example of analysing the product footprint and taking action. Ideally, we also want to reduce CO2 emissions from transporting scrapped wheelchairs to the factory. However, reusing aluminium already gives us such a CO2 advantage. We are pleased to work closely with Etac towards a sustainable future and hope others are inspired to join us.
FEMKE VISSER
SUSTAINABLE PROCUREMENT, MEDUX
For more information about the re:vive concept, please contact:
Marika Törnqvist
Head of Product Management, Etac wheelchairs
marika.tornqvist@etac.com